IO-Link brings continuity of information from the sensor level to the automation and web worlds.
IO-Link is certainly one of the shooting stars of automation technology. In recent years, the vendor-neutral plug-in connection has established itself in many applications due to its simplicity, ruggedness, and low cost. But there’s more to IO-Link. For one thing, IO-Link is an enabler for innovative sensors. For another thing, IO-Link ensures the data availability demanded by Industrie 4.0 and Industrial Internet of Things.
Ever since Industrie 4.0 and its subset, Industrial Internet of Things, became top topics, manufacturers of automation components have had to confront the challenge of harmonizing the automation technology world with the Internet world. Industrie 4.0 is based on global availability of all relevant information. Generally, it is sensors that supply this information. Sensor manufacturers thus face new challenges but also have unforeseen opportunities. On the plus side: With the development and establishment of IO-Link, sensor manufacturers have done the groundwork in the best way possible so that Industrie 4.0 approaches can be easily implemented.
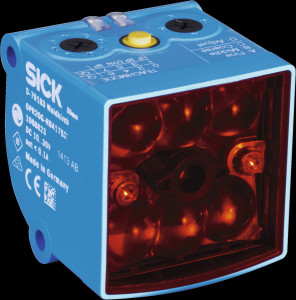
In recent years, it is not only Internet applications that have undergone further development. Sensor technology has also advanced with giant steps. If sensors were mainly used in the past for switching on and off or to provide distance values, a new class of sensors is now taking center stage. These often cover 10 or even 30 parameters and are very intelligent (photo 1: SICK Sensor “Glare”). Instead of providing switching information only, they offer solutions for processes like condition monitoring. For example, a sensor may currently be able to not only detect an object but also to indicate how well it has detected this object. Based on this, a cleaning process can be initiated for the sensor at a value of 80 percent. Another trend: sensors are becoming subsystems that no longer consist of sensors only but also have actuators on-board. Here too, interesting developments from the field of condition monitoring already exist. For example, in the case of pneumatic actuators containing pressure sensors, the pressure characteristics are checked and compared with past pressure characteristics. If changes arise (even creeping changes), early intervention is possible.
System-independent device engineering
The resulting demands on sensor manufacturers are multifaceted. For example, these types of subsystems require their own engineering tool and operator interface that can be used to match the device to the respective application level. A PLC, as we know it today, cannot perform the engineering. Nor is it able to adapt the subsystem to the respective application. The controllers merely provide a selection of compiled and filtered information to higher-level system solutions such as SCADA (Supervisory Control And Data Acquisition) or MES (Manufacturing Execution System) systems.
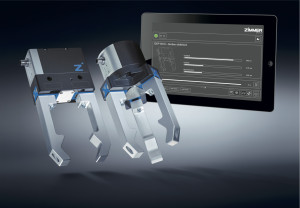
Often, this is not desirable because the subsystem manufacturers have inserted a lot of know-how in their products, which they obviously want to protect. One example of such a subsystem, which is already equipped with its own setting wizard app, is an electric gripper for handling tasks. The user can not only set up the gripper using the app but also select various device views for service technicians, operators, and the engineering team, for example. It is crucial for sensor manufacturers and users that this setting wizard can function independently of the system. Single-cable technology is another requirement. The electric gripper has only one cable that transmits both power and data (values of pressure and temperature sensors, distance measurement, etc.)(photo 2: Zimmer gripper). This development was made possible by IO-Link.
Reliance on standards
IO-Link uses 3-core unshielded standard cables and replaces inflexible special cables and application-specific wiring. IO-Link users can typically make use of a standard plug-in connection (M12) and cable even for complex sensors with multiple signals. Slim 3-core cables can be routed in a space-saving manner, have smaller bending radii, and are also available in a trailing cable-compatible variant.
Interest in IO-Link is based not only on its simple cabling. Another reason is its continuity from the control level through the automation level (fieldbus/Ethernet) to the Internet. Industrie 4.0 will not be possible without standards and continuity. While the world has long agreed on technology (HTML5, CSS3, and Javascript) on the Internet side and only one system-neutral technology (IO-Link) exists at the base level, there is currently a colorful variety of technologies at the intermediate level.
IO-Link easily meets the demand for standardized continuity. Over 100 companies around the world have already implemented the IO-Link standard in their components. The system-independent communication standard for the lowest field level provides a system-wide cyclic data channel (process data) and acyclic data channel (parameters and diagnostics) down to the smallest sensors and actuators. As a component of the internationally recognized standard IEC 61131 (Part 9), IO-Link is associated with control technology and not fieldbuses (IEC 61158 and IEC 61784). As a result, the point-to-point connection can be integrated in all fieldbuses worldwide and is not tied to manufacturer-specific systems.
Even if many users describe direct continuity between the automation world and the Internet world, the reality is (often still) something else. Currently, data switches are often integrated after the sensor level (IO-Link) that steer the data to the automation world or the web world. IO-Link operates independently of this – through its simplicity it delivers information to both worlds.
The manageable costs of IO-Link have also contributed to its huge success. Often underestimated is the fact that almost everyone who thinks about Industrie 4.0 today connects this with Ethernet technology. But, because of cost or space restrictions, not every sensor in a factory will have an Ethernet interface. Problem-free integration of an IO-Link interface is also possible in price-sensitive or tiny components based on the very low implementation and component costs.
Enabler for innovative sensors
It is also apparent that entirely new opportunities for sensor development are coming into play and IO-Link will be the enabler of new applications. For example, signal lamps are being developed that would not exist without IO-Link. Normally, there are two wires per color in signal lamps. The more colors there are, the thicker the cable will be. In this signal lamp, various segments can be individually used in different modes. The conventional signal lamp thus becomes a flexible display instrument that can visually indicate the stacking height of packages; for example, to wire this lamp conventionally, an 80-core cable would theoretically be needed. With IO-Link, this lamp is a device like any other. The result is that many lamp manufacturers have implemented the M12 connector as a standard feature in their internal specifications.
Outlook
Another interesting aspect: all setting parameters as well as high-quality information available through an IO-Link device are described by the powerful device description (IODD) and accessible to all software tools (all the way to the cloud). Together with the worldwide unique device identification, this enables consistent interpretation of parameters and data. Thus, IO-Link devices can not only be easily parameterized but APP-based user interfaces and interfaces to cloud services can also be easily generated. This provides new capabilities relating to plant availability and condition-based maintenance and opens up additional potential.
Industrie 4.0 offers many opportunities – without continuity, however, many ideas are not feasible. The IO-Link technology with its ability to communicate down to the lowest field level is thus seen as the key to the digital factory. The greatest advantages of IO-Link include its simplicity, the fact that there is no system break with the existing switching technology, and its vendor neutrality. As a result, the entry – including into the Industrie 4.0 world – will be made significantly easier.
Author: Frank Moritz, SICK AG, Leader of PI Working Groups “IO-Link Technology” and “IO-Link Quality”