Since the very beginning, PI has always developed standards in close cooperation with users. “First we have to find out what it is that users want. Only then can joint solutions be devised from this and products which have been tried and tested in practice finally created,” remarked Xaver Schmidt, Head of the PI Industrie 4.0 Working Group. This was also the case with OPC UA work. “We had decided on this technology long before there had been so much talk about OPC UA in the market,” commented Schmidt, who promptly followed this up with an explanation. “PROFINET wasn’t developed for tasks like those currently covered by OPC UA.”
Background information: With OPC UA, object modeling can be mapped from a variety of different data sources, but this information has to be supplied first. “This is precisely the task handled by PROFINET. Plus, we aren’t the only ones using OPC UA – robot controllers and IO-Link use the technology as well. All this information from the individual components can easily be tapped at the same time on a PROFINET network,” continued Schmidt. The user can already install additional Ethernet devices at any desired point on a PROFINET network at any time. PROFINET’s openness thus makes it possible to also add more complex sensors or devices with an OPC UA interface which send their values directly to corresponding cloud services or edge gateways without needing to tediously reconstruct the automation solution.
Creating Precise Maintenance Plans
Asset management information – that is, specific information on which devices are installed, their versions and their status – is especially sought after. “This sounds boring at first,” admits Schmidt, “but it’s unfortunately true that many users simply don’t know which devices with which hardware and software versions have been installed in a system over the years.” Without this kind of information, however, maintenance plans can’t be created – let alone asset management or more advanced diagnostic functions.
OPC UA alone is not able to provide this kind of data for use in practice. The 30 million devices in the field with a PROFINET interface are able to do this very well and have been able to do so from the very beginning of PROFINET using the corresponding identification & maintenance services, for example. This is why PI and the OPC Foundation have been working for some time on shaping the way PROFINET and the OPC UA interact to make getting started easy for the user.
Different Viewpoints
What looks easy to the user after the fact actually involves a wide range of work on the part of both organizations. From a technological viewpoint, the production data and process flows of a machine are important, whereas the devices in use are interesting from a maintenance perspective. The PROFINET viewpoint deals with presentation of the devices, a network facet takes care of interfaces & ports and a functional facet handles a control loop, for example. These different ways of looking at the same machine have to fit with one another and be reference-able. The viewpoints which are crucial for day-to-day operation were developed jointly by PI and OPC UA using multiple use cases.
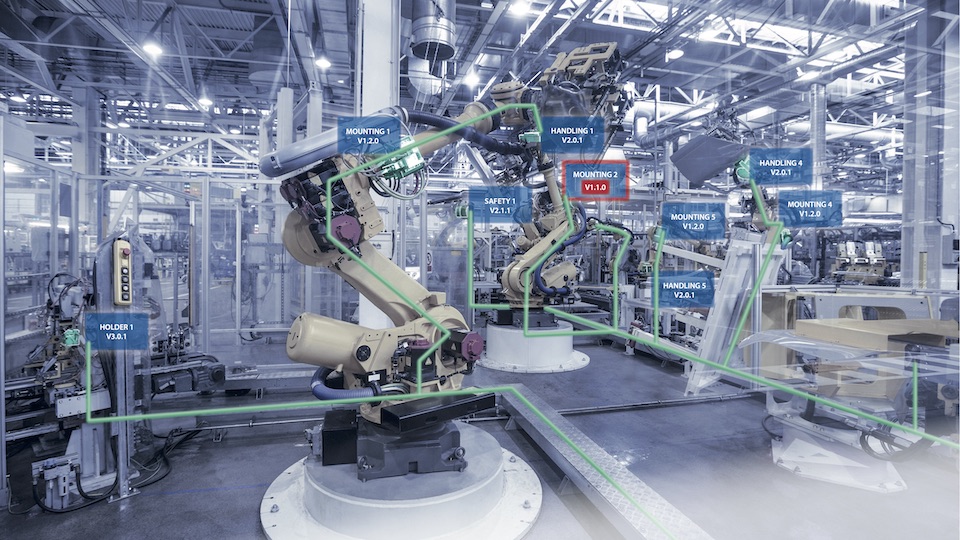
According to Schmidt, “It was important to us to not only be able to cover the PROFINET viewpoint with the current solution, but the functional viewpoint including cross references as well.” In addition, energy management requires other information just as much as details on networks. Separate working groups which deal with these topics in more detail were founded for this purpose. Schmidt is aware that, “As a result, the expenditure required for this initial version of the OPC UA-PROFINET companion specification was certainly greater than could be deduced from just the PROFINET map.” The work was worth it, however, as it laid the foundation for an overall solution appropriate for the application. The joint OPC UA – PN companion specification version 1.0 is now available for download.
Examples of Use-Case Implementation
The fact that this approach works in practice has already been shown by the proof-of-concept trade fair model, which incidentally was demonstrated on fairs. A variety of different use cases, from controller-to-controller mapping to energy management to the NOA (Namur Open Automation) connection of actuators, show that a broad range of applications are covered. Individually, they include:
- Controller-to-controller with multiple vendors
- PROFINET OPC mapping in PLC
- PROFINET OPC mapping in edge gateway
- PROFINET OPC mapping in device
- Mapping IO-Link
- Vendor-specific OPC UA model
- Multifaceted model
- Namur Open Architecture (NOA)
Outlook
Combining OPC UA and PROFINET makes an optimized, future-proof solution possible. The most important feature is undoubtedly the standardized mapping of existing, reliable data from PROFINET on OPC UA. This doesn’t mean that all the work is finished, though. Work is currently being carried out to integrate PROFIenergy. The automatic switching on and off of devices and components, as opposed to continuous operation, became established at production operations long ago. Now the focus is on accessing individual measurement values across multiple manufacturers – the foundation of higher-level energy management. “This is where our experience comes in. We’re able to access existing use cases here and work closely together with measuring device manufacturers,” said Schmidt of the current state of affairs.
To PI, having a user-friendly and future-oriented network on which both existing and new technologies function smoothly alongside and with one another like cross-manufacturer solutions is a stated goal. Development of the OPC UA-PN companion specification version 1.0 again serves as a good example for how a practical solution can be devised as a response to a demand from the industry.