Industrial robots are increasingly taking over tasks that were previously reserved for machine tools or special-purpose processing machines. For this reason, users are calling more and more for the consistent integration of robot systems in machines with respect to handling systems, function, and communication technology. This can be achieved with the help of PROFINET.
Consistent Integration
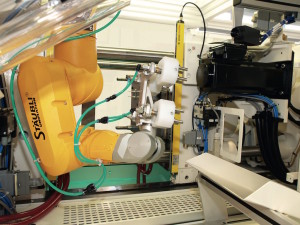
The more frequently robots become standard components of a larger machine, the more they will have to be adapted, together with their control and handling systems, to the machine concept and be fully integrated in this concept. System integrators avoid the additional effort for this type of adaptation. End users are also no longer willing to deal with two different systems for the machine and robot. The solution would be to integrate the robot(s) and related control system in the machine as a stand-alone functioning subsystem and to utilize only the familiar operator interface of the machine for all functions. The objective is for the robot to effectively become an invisible component of the machine as far as the operator is concerned. The more consistently and easily this type of integration can be carried out, the greater the participation of robots in the machine building market will become.
The most important requirement for this is the integration of a uniform communication system within a machine or system. This means: minimal or no interfaces in the field and to the corporate level. Moreover, the communication technology must meet the stringent speed and clock accuracy requirements for motion control tasks while maintaining a high level of acceptance as a standard for all other manufacturing and process automation tasks. PROFINET offers the solution for this. Thanks to its scalable performance classes and its application profiles, this Industrial Ethernet bus system has become the leading universal bus of automation technology, including drive applications, and not just for motion control applications.
Flexible Concept
Machine builders want support from their suppliers in the form of pre-configured subsystems for a requested application that can be integrated in the machine without significant effort. This is a significant departure from their earlier preferred practice of purchasing and installing the robot components themselves. The uniVAL concept developed by the robot manufacturer Stäubli allows flexible and easy integration of a robot system into a higher-level control system. The key to this is a special operating mode of the Stäubli CS8C robot controller in which the axes of the connected robots are handled by the higher-level control as separate network nodes. The controller is connected to the PROFINET with IRT communication network of the machine via a configurable PCI card and then forms an open interface to the real-time communication systems. A robot, together with its controller, is thus fully integrated in the machine.
Consequently, there is only one operator interface and only one programming language and environment, namely those of the machine or the machine controller. The higher-level machine controller takes over the functions of the application, route planning, set-point positions, and travel commands, while the uniVAL-Drive, as a sub-controller, concentrates on the closed-loop control algorithms of the axes, such as synchronization algorithms and logical axis decoupling algorithms, as well as on the motor control and drives.
Everybody Wins
The concept was developed with intensive support of PROFIBUS & PROFINET International and its member companies. The NetX technology from Hilscher was relied on for development of the interface to PROFINET with IRT and for implementation of the PROFIdrive drive profile (Application Class 4).
Conclusion: Machine builders and system integrators can implement increasingly more universal machine concepts, thereby lowering costs and winning new customers. At the same time, robot manufacturers will be increasingly seen as attractive suppliers of machine builders and can generate growth from this. In the end, plant owners receive machines that combine the latest control technology, Industrial Ethernet communication (PROFINET), and advanced robot expertise in a single unit.