AWL-Techniek’s M-Line series makes it a trailblazer in the modularization of production lines. Turck was able to optimally support the Dutch machine builder with a decentralized safety concept with IP67 protection. The combination of IO-Link and hybrid safety I/O block modules saves a lot of wiring work because the entire safety architecture can be installed outside of the control cabinet. The consistent galvanic isolation of the sensor and actuator voltage enables the decentralized safety disconnection of actuator groups on the I/O hubs with IO-Link. The binary interface supplies valuable diagnostic data for Lyla, AWL’s dashboard solution for displaying and evaluating the data. The project proves how modular machine construction can create flexibility and shorten lead and commissioning times.
Anyone designing a kitchen in an online configurator will experience modularity par excellence. The individual modules here consist in turn of modules for the side panels, the base panels, rear panels and drawers. At the end of the process you can choose the fronts and front panels from different styles, a handle design and a matching worktop.
The example of the DIY kitchen shows clearly that modularity is inconceivable without standardization. Only when the clearances, dimensions, drill holes and connections for water or gas are defined can the benefits of a modular production strategy be used: a large range of variants and great flexibility with short lead and delivery times and moderate prices.
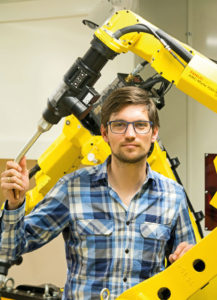
Matthijs Varwijk uses these and other arguments to persuade interested prospects and customers about the modular machine concept. Varwijk is an R&D project manager and is also responsible for the modularization strategy at the Dutch machine builder AWL-Techniek situated in Harderwijk. With over 750 employees at five sites worldwide, AWL has made a name for itself with its automated welding and connection lines, particularly in the automobile sector. Major car builders, suppliers and many other customers worldwide use the machines of the Dutch company in their production lines. An interdisciplinary team around Varwijk implemented modularity in AWL’s machine portfolio in 2017 and gradually defined the standards of the M-Line. This initially required some persuasion in-house. Particularly in the transition phase from the conventional to the modular production layout, the benefits are not always clear to see. Standards have to be defined first of all, and this often also involves a lot of restrictions.
Frameworks Create Flexibility and Save Costs
The first standard set by AWL was the name of the product series: The M-Line represents a modular product series as well as standing for “line” as in “production line” in which the individual modules are combined. The basis of each module is the rectangular steel frame, which is designed to fit inside an ISO container. This saves time and costs when transporting and commissioning the machine. The customer can also expand or convert the system easily at a later time since the modules can be rearranged again in the production hall using suitably designed fork lifts.
Modularization Needs Standards
Besides the basic frame, three central module types were defined from which the M-Line is to be built: an operator module, in which a worker can insert components and start processes, an indexer module, which consists of turntables or other devices for handling the workpieces, and a process module, which processes workpieces, such as with welding robots or machine tools.
The Aim: an Empty Control Cabinet
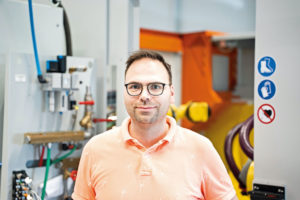
AWL benefited here from Turck’s Ethernet multiprotocol technology for I/O modules. It enables the manufacturer to use identical IO block modules in each M-Line module – regardless of whether the customer prefers a PROFINET controller or otherwise. “We wanted as many standardized components as possible and also a largely standardized control cabinet. Ideally, we will one day just have a PLC and a power supply unit in the control cabinet,” Jasper van Kooij announced. We haven’t got there yet but there is already a lot of air in the control cabinet of the AWL modules. This is also helped by Turck’s IP67 I/O hybrid components for standard and safety signals.
Impressive IP67 IO-Link Safety I/O Concept with Scalable Safety Technology
AWL was impressed by Turck’s concept of a modular IP67 IO-Link safety solution: The core of the solution is the TBPN hybrid safety I/O module. This comes with an integrated safety controller which can talk to the PLC via PROFIsafe over PROFINET. The module is provided with four safety I/Os, two conventional digital I/Os and two IO-Link ports. The TBSB safety disconnection box, which safely switches off the actuator voltage V2 in a serious situation, is connected to one of the safety I/Os.
The power supply for all modules runs likewise via the safety disconnection box. This ensures that no actuator is supplied with power, for example, in the event of an emergency stop and nothing can move anymore in the machine. The sensors remain active as these are fed via V1. In this way the machine is always visible in the controller. The digital sensors and actuators of the welding cap cutters are connected to IO-Link hubs, which in turn communicate with Turck’s TBEN-L-8IOL IO-Link master. The IP67 block provides four IO-Link ports in accordance with the Class A and four in accordance with the Class B standard. This separates the voltage for the sensors (V1) from the actuators (V2). In this way the safe disconnection of the power supply is ensured also via IO-Link.
IO-Link Boosts Standardization
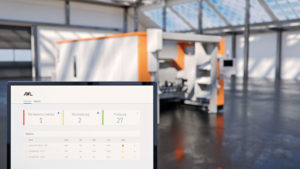
The use of the IP67 solution including safety and I/O hubs with IO-Link saves AWL a lot of wiring work. As IO-Link devices, the hubs transfer the digital signals of actuators and sensors in the IO-Link protocol and bring them to the IO-Link master, where they reach the controller via Ethernet. For van Kooij and Varwijk, another reason was the fact that the bidirectional interface boosts the standardization of the M-Line. The safe signal transfer via three-wire cables eliminates the need for specially shielded cable types and special cables. IO-Link also ensures higher availability of the machine: The Lyla dashboard system is part of the M-Line. This collects the data of different machines, evaluates it and thus monitors the operation and performance of the machine. This is also possible through the use of diagnostic data via IO-Link.
Scalability Speaks for M-Line
The modularization of the controller level has not yet taken place. Every control project so far still has to be started from scratch and only function blocks can be reused. The modularization project is anyway never finished. The M-Line is being very well received by AWL’s customers. They consider the scalability of the machines to be a major benefit. Replacing an operator module at a later time with an automated solution in order to increase output is not a problem. It’s just like with kitchen units: When you move, you simply take the kitchen units with you and add a few modules.