Standardized wiring and electronic name plate support commissioning and increase availability.
In almost all industries, machine users require increased flexibility for production means for small batches and continuous diagnostics of all actuators and sensors to increase availability. In addition to this, there is quickly increasing horizontal and vertical connection of machinery and systems for Industry 4.0 applications. The open standard IEC 61131-9, IO-Link, fulfills these requirements at low connection costs and energy consumption. The flexibility of hydraulics is increased by the transmission of parameter changes during running operation. The provision of diagnostics information offers numerous opportunities to extend the concepts of predictive maintenance for hydraulics to increase the availability of systems and machinery. The manufacturer-independent IO-Link interface can be integrated easily and quickly in any industrial automation application.
Introduction: Limits of Serial Fieldbus Communication
The introduction of fieldbus technology in the 1980s was the starting point for horizontal connection of decentralized actuators within machinery. Serial wiring lead to a considerable reduction in cabling and opened new possibilities for modularization in mechanical engineering. Fieldbuses as well as most current real-time Ethernet protocols, have been developed by control system manufacturers and focus on communication between electric control systems and selected peripherals. For actuators, sensors, and other third-party equipment, either their manufacturers or system integrators are required to provide suitable interfaces in hardware and software for the respective fieldbus. This can be very complex as device profiles and software have to be created in the respective PLC for every individual fieldbus and control system of each manufacturer.
Possibilities for Hydraulic Connection
The integration of hydraulics in modern automation systems can be realized in different ways. Numerous existing machine concepts apply on-board electronics for the control of hydraulic valves. The exchange of digital information is restricted and only possible if the respective device is connected to a superior control system via individual wiring. This technology no longer meets the requirements of end-users.
The alternative are valves with integrated fieldbus connections. These, however, require extensive wiring as well as integration into the control system and the respective fieldbus protocol by means of dedicated software. Both require considerable effort that is too high for price-sensitive applications.
Thanks to IO-Link, machine manufacturers and system integrators are able to integrate, for example, proportional hydraulic series valves and sensors into digital communication structures with very little engineering effort. With its simple communication structure, IO-Link has low hardware requirements. Additionally, the standardized M12 connection technology enables simple and cost-efficient connection of hydraulic valves in the field. This way, previously “deaf-mute” components with analog control are transformed into communicative and flexible actuators and sensors.
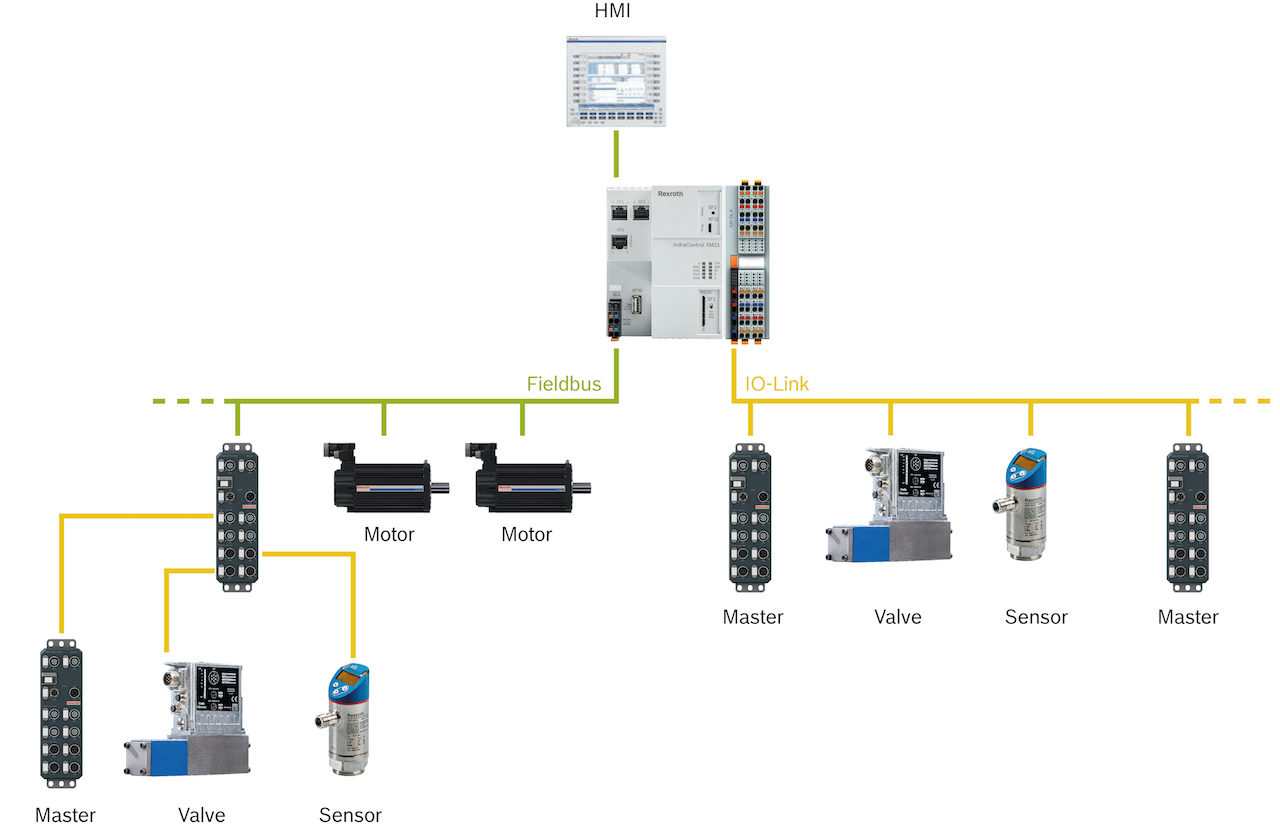
IO-Link: Manufacturer-Independent and Compatible with all Fieldbus Protocols
The manufacturer-independent IO-Link interface, according to IEC 61131-9, standardizes connection technology for actuators, sensors, and other equipment and provides a digital communication protocol for data exchange between control systems and devices regardless of the fieldbus. Fieldbus technology is not replaced –but extended. Parallel communication enables machine manufacturers to use IO-Link with all protocols and integrate IO-Link-compatible devices into various machine concepts without additional effort.
IO-Link is currently already supported by around 130 device manufacturers and companies. IO-Link Masters are offered by around 40 manufacturers, and the standard is supported by nine manufacturers of control systems with central Masters and respective engineering tools. IO-Link devices are in the product range of almost sixty manufacturers of sensors, actuators, and other peripherals. Rexroth, for example, now also offers hydraulic proportional valves and pressure sensors with IO-Link technology. The function and performance of these proportional valves are identical to series valves. However, they also offer all options for bi-directional communication via IO-Link. This way, the hydraulics can be integrated seamlessly into connected structures. Parameters and operating states can be changed by the control system during running operation.
IO-Link System Set-Up
A full IO-Link system consists of one centralized or decentralized IO-Link Master, one or more IO-Link devices as well as unshielded 3 or 5-wire cables with M12 connectors. Project planning and parameterization of the IO-Link Master can be realized in the control system hardware or an optional engineering tool. The point-to-point connections between IO devices and the automation system are established by the IO-Link Master. It serves as the interface to the superior control system.
IO-Link Masters are offered for the connection of one IO device per port. The selection includes options for IP20 control cabinet as well as decentralized modules with protection class IP65/67 for installation on machinery. Particularly in large-scale systems, cabling is considerably reduced.
For decentralized IO-Link Masters, the user organization of IO-Link has defined M12 plug-in connectors with three or five conductors. The 5-pole version “Class B” port is used for devices with increased current consumption like hydraulic valves. The 3-pole version “Class A” port provides an energy supply of up to 200 mA which is sufficient for most sensors. In contrast to analog controls, unshielded cables are sufficient for fault-free communication over a cable length of up to 20 meters. IO-Link standardizes the connection technology for all actuators and sensors and eliminates numerous sources of error during the installation of systems. Otherwise, complicated and expensive cable dimensioning with individual wiring and shielding is no longer required. The logistic effort is reduced thanks to the application of uniform cables.
Rapid Commissioning per Software
Every IO-Link device features an electronic device description, referred to as IO Device Description (IODD) file. It provides standardized important information:
- Device data
- Text description
- Identification, process, and diagnosis data
- Communication properties
- Device parameters with value range and a default value
- Image of the device
- Logo of the manufacturer
The IODD file syntax is identical for all devices of all manufacturers. The IODD file enables automatic recognition of the device by the IO-Link Master for immediate parameterization. Also, device descriptions are automatically included in the system documentation.
For project integration of the IO-Link Master into the overall automation, commissioning personnel use the engineering tools of the respective PLC manufacturer. The IO-Link Master is selected from the device portfolio and added to the overall automation. Depending on the control system manufacturer, all blocks for communication are available via a library for free.
Via IO-Link to Industry 4.0
IO-Link enables access to device data either directly from the control system or remotely via networks from any location. Particularly important for future-oriented concepts: Already today, IO-Link offers type and instance data of Industry 4.0 devices according to the definition of the German “Plattform Industrie 4.0” initiative.
This way, hydraulic actuators also meet all conditions for future requirements of Industry 4.0 applications. Additionally, this approach is well-suited for subsequent connection of existing machinery and systems with minimal effort.
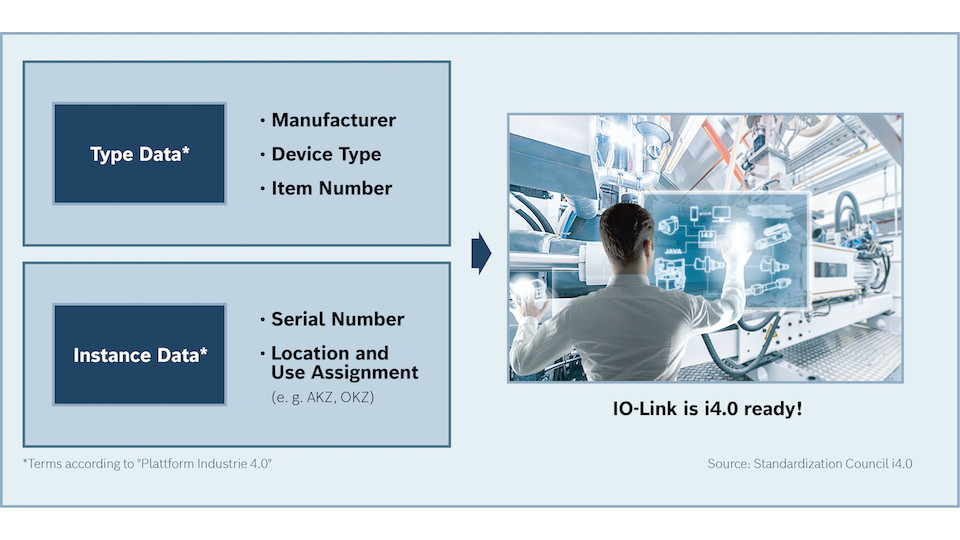
Diagnosis Functions for Increased Availability
The diagnosis functions of IO-Link devices enable new maintenance concepts and considerably reduce repair times. Now possible, the call-up of device information in parallel to the process data, forms the basis for condition-oriented and predictive maintenance concepts. In this respect, proportional valves report whether they are functional as well as errors like under- or over-voltage and electronic temperatures exceeding an admissible value. In addition, the valve and sensor status is displayed for transparent error analysis. An integrated operating hour indicator enables calculation of the residual life cycle for maintenance and decision-making on further use of the valve.
In case of faults, IO-Link accelerates diagnosis thanks to remote access for maintenance technicians to identify the type and location of any errors. Precise localization without actual presence at the system considerably reduces reaction times. If necessary, the maintenance technician opens the IODD file of the respective device in the control system. Compared to before, components do not need to be disassembled to decipher hardly readable labels, and manufacturers and types no longer need to be looked for in system documentation. Thanks to an electronic name plate, all this information can now be accessed with just one mouse click to initiate the respective order without delay.
IO-Link follows the plug-&-play principle. Replaced devices are recognized by the IO-Link Master according to their IODD file, and the respective parameters are automatically transferred without any action in software. This way, even inexperienced technicians are able to replace components without problems to considerably reduce system downtime.
Summary
The open IO-Link standard establishes continuous communication with sensors and actuators irrespective of the fieldbus used. Even hydraulic proportional valves can be intelligently, easily, and cost-effectively integrated with bi-directional digital communication. This simplifies commissioning in hardware and software and enables flexible adjustment of hydraulic valves for varying production processes. Increased requirements for flexible machinery and systems are now complied with. Comprehensive diagnosis information enables condition-oriented and predictive maintenance concepts, and standstill and maintenance times are reduced. This increases the availability of machinery. In addition, IO-Link enables future-proof integration of hydraulic valves into connected structures as Industry 4.0 components with all their related features.
Technical Article submitted by Bosch Rexroth AG