A renowned manufacturer of sophisticated mechatronic products relies on RFID technology integrated into production processes via IO-Link. The manufacturer utilizes this technology in the – for the first time – modularly designed module and final assembly of the power electronics units for premium electric cars. The mobile data storage devices are suitable for the increased temperatures encountered during casting.
With the power electronics unit, the Zollner Elektronik AG manufactures and assembles the electronic heart for a well-known electric car series at its headquarters in Zandt, Germany. To this end, the mechatronics service provider has constructed a modularly structured module and final assembly in a clean room.
RFID technology from Siemens contributes to the perfectly coordinated process flow across various manual and partially automated workstations. Crucial for the selection of the Simatic RF200 system in the IO-Link interface variant in conjunction with mobile data storage devices of the type MDS D160 were the easy connection to the module controllers, the low system costs, and the high temperature resistance of the tags.
The clean room houses the printed circuit board production utilizing surface-mount technology and/or through-hole technology (SMT/THT) followed by the module assembly and final assembly including various inspection and testing stations. Zollner has chosen a modular design for the lines throughout with independently controlled stations that can be employed flexibly and later be modified easily for continued use. Reliability and durability in conjunction with the availability of replacement parts were important aspects in the selection of all components.
Tracking and Tracing
Altogether, there are about 100 reading points in the module assembly and final assembly production flow control and for the immediate documentation of every completed step in overlaying databases. “For us as well as our end customers, quality is the top priority, which has to be fully documented and traceable across all processes,” says Bernhard Kirst, director marketing at Zollner. Because effort and costs have to stay within competitive limits, the readers Simatic RF210R with integrated IO-Link functionality from the HF RF200 product range by Siemens were selected. They enable a connection to any controller complying with the IO-Link standard. The control system employed by Zollner offers a suitable IO-Link master module for that. The screw-type readers (M18 x 71 mm) with integrated antenna automatically supply the data read off transponders – here the unique identification number (UID) of the respective workpiece carrier. At the start of the line, the workpiece carrier is “married” to the base module of the power electronics. By means of the UID, the assembly is identified at every station, the required process step initiated by the controller, and for manual workstations, work instructions displayed to the employee. Relevant production data are immediately written back to the databases. Tracking and tracing data are thus constantly collected, documented, and archived.
Transponder for increased Temperatures
The compact and extremely rugged HF readers with IP67 protection rating employ the radio interface protocol in accordance with ISO 15693 and can, in principle, read from and write to all standards-compliant mobile data media. Every time the transponders pass through the casting facility, they are subjected to a temperature of 100 °C for at least 20 minutes. “Not all transponders are capable of doing that on a continuous basis, and at a low price to boot,” says the responsible electrical and software planner Andreas Meidinger. One that can do that without limitations is the mobile data storage device MDS D160 by Siemens. The ISO-compliant, hardened transponder is designed for use at temperatures up to 175 °C and has proven itself in industrial laundry facilities and other thermally demanding processes. For easy mounting, Zollner installs the chip-shaped transponders (Ø16x 3 mm) in plastic spacers. They are affixed either into the bottom or at the side of the circulating workpiece carriers. Two workpiece carrier variants each are in use for the charger and DC/DC converter assemblies – a simple one for thermally uncritical stations and one for increased temperatures for casting only. A robot automatically relocates the assemblies.
Proven in Practice
Zollner Elektronik AG has been manufacturing power electronics units since the end of 2012 – without a failure or malfunction. The RFID combination of reader and transponder selected has proven itself in daily operations and is now also being employed or specified for many other assembly systems. “In this instance, support from the supplier was not necessary, since all components are easy to use and – thanks to the IO-Link standard – can be integrated into a wide variety of controllers,” states Andreas Meidinger.
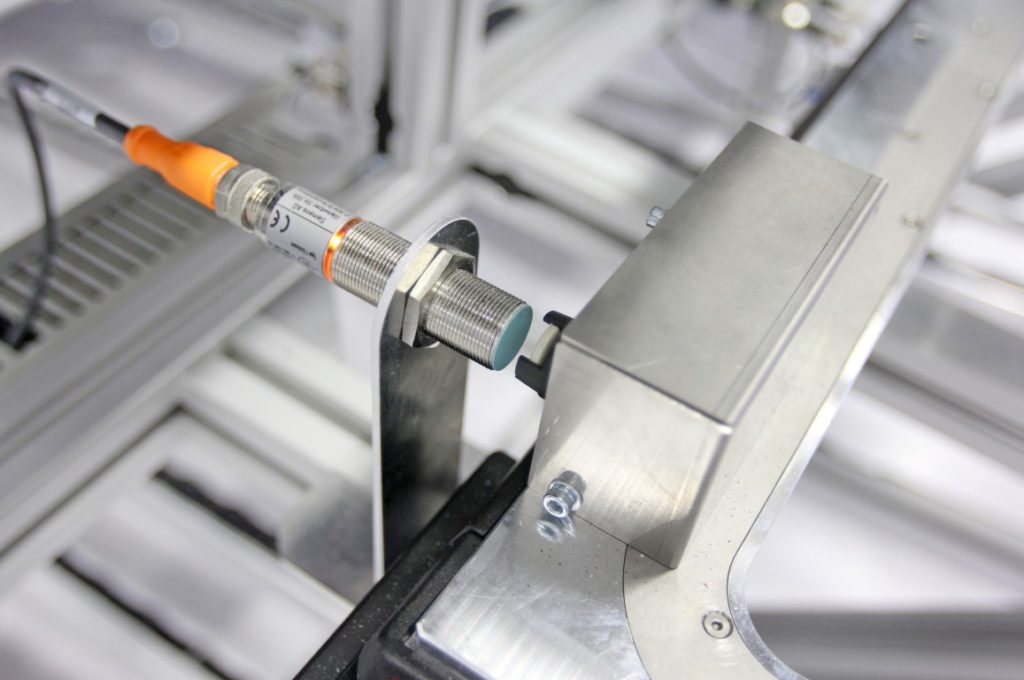