Buzzwords such as Industry 4.0, IIoT and BigData are on everyone’s lips and it feels as if industrial automation is currently experiencing a new megatrend. There is a lot of talk about new, so far unimagined possibilities that are not only technologically challenging, but also some kind of a dream – such as the much-discussed batch-size one. All these aspects will first have to develop over several stages of evolution. Nevertheless, what about the elementary basis for these future visions – the wiring philosophy?
While a control cabinet used to be the central element of automation, automation technology is now becoming more and more decentralized in the field. That means there are many small automation islands throughout the plant. This changes the wiring philosophy decisively: While it used to be standard for large cable bundles to run centrally from the control cabinet into the system, today it is common to realize serial wiring via bus technology. Wiring via bus technology has had a lasting effect on automation and has optimized the wiring effort. Only the power supply stuck to the central wiring approach for a long time. However, new standards such as «M12-Power» now allow the power supply to follow the network wiring. This structured network wiring for power and bus can be excellently described as «Power follows Bus».
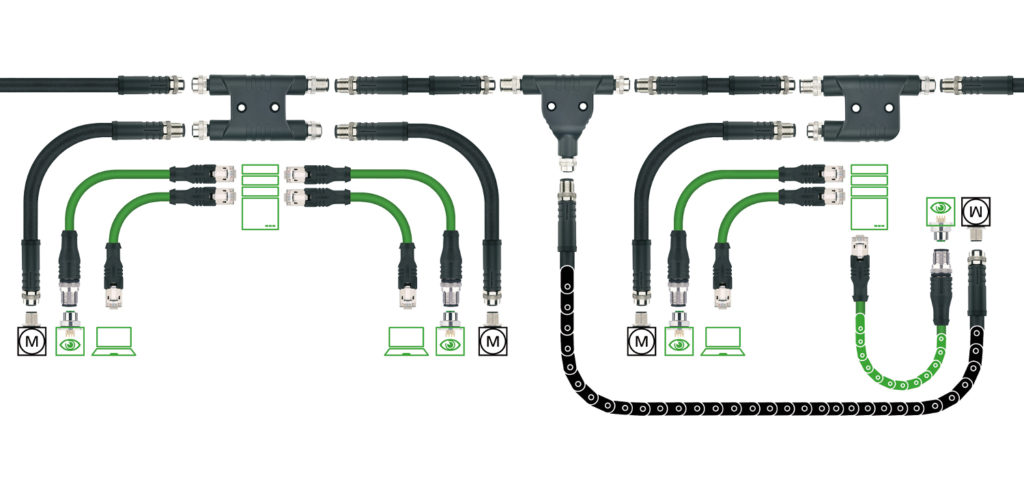
Home Network and Industrial Network Are Not the Same
The network forms the backbone of automation. Today’s and tomorrow’s requirements and technologies cannot be implemented without intelligent communication. Increasing data volumes and ever-increasing speeds in data transmission can already be observed today. Mainstream technologies from the consumer sector, such as Ethernet, are also conquering ever-larger areas of automation – even though these technologies first have to be made suitable for automation. Especially in terms of speed, determinism and network availability, consumer technology cannot be transferred to automation one-to-one.
Nevertheless, not only the network availability, but also the environmental conditions in the automation industry differ fundamentally from those at home. Connectors and cables are therefore of crucial importance. While the cable must be resistant to e.g. oil and chemicals, prevent interference and at the same time master flexible moving applications, it is important that the connector is robust and can have a high degree of protection. With the constantly increasing demands on network performance, the quality requirements for connectors and cables are also increasing.
Wiring is the Foundation for Industry 4.0
Interfaces are the potential weaknesses in every wiring concept. If the number of interfaces increases, the number of potential weaknesses also increases automatically. These weaknesses can be significantly reduced with high-quality connectors, while at the same time the performance and availability of the overall network are increased. Within a connector, the shield connection, the shield transfer as well as the wire assembly and the wire routing each have a major impact on the performance. With the patented two-shell shielding concept (2SSK), ESCHA has developed an ideal technology that shows its strengths especially in border areas. The cable shield is crimped directly onto the shield halves using a crimp ring, without deforming the cable. The wires are thus routed in their original stranding to the connection point on the connector. As early as the development phase, both the connector and the contact were designed in such a way that they do not create any asymmetries in the overall system.
While current industrial communication networks are still reasonably fault-tolerant, future production processes such as those envisaged in Industry 4.0 can only be implemented using safe and reliable wiring. It is therefore advisable to rely on high-quality connectors at an early stage in order to align the network structure to future requirements.
Structured Power Distribution via M12
Meanwhile, the new standard called «M12 Power» allows the use of the industry-proven M12 connectivity for power distribution in the field. The normative basis IEC61076-2-111 distinguishes between DC and AC voltage applications and the number of pins.
DC-applications | ||
T-coding | 4 pins | 63V/12A |
L-coding | 5 pins (4+FE) | 63V/16A |
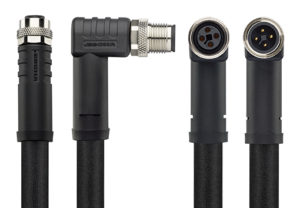
AC-applications | ||
S-coding | 4 pins (3+PE) | 630V/12A |
K-coding | 5-pins (4+PE) | 630V/12A |
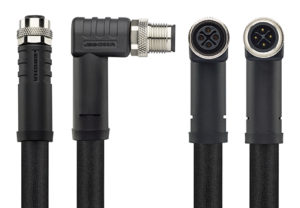
In addition to overmolded connectors and field-wireable versions, there is also distribution technology designed for the special requirements of power applications. Structured bus wiring has only become possible with this distribution technology. While T-junctions have been in use in the field of sensor technology for a long time, ESCHA has developed a T-junction as well as an H-junction (one feed, three outlets) and an h-junction (one feed, two outlets) for the typical power codings. Essential features of these M12 power products from ESCHA are connectable cross-sections from 1.5mm² to 2.5mm². These cross-sections ensure a low voltage drop, especially in the case of DC-distribution, and therefore enable a large expansion of the power distribution.
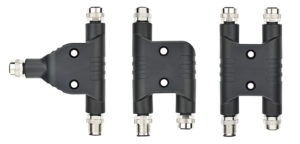
Conclusion
If you want to be prepared for future technologies and trends, you will already find a good basis for connectivity today. If you are already paying attention to the qualitative differences in the base, you can sit back and relax. Because the infrastructure is still powerful enough – even at the limits of future technologies – to ensure high availability and robustness without network failures or loss of performance. Power and bus can run through the system with the currently available components in the same structure. All of this forms a structure that places Industry 4.0 on a secure foundation.