Solland Silicon in Meran, Italy, is one of the leading companies in silicon manufacturing for the photovoltaic industry. The factory in Meran, Italy, belongs to the PUFIN Power Group and is a chemical manufacturing operation. They have used PROFIBUS since the 1990’s and now use PROFINET as well.
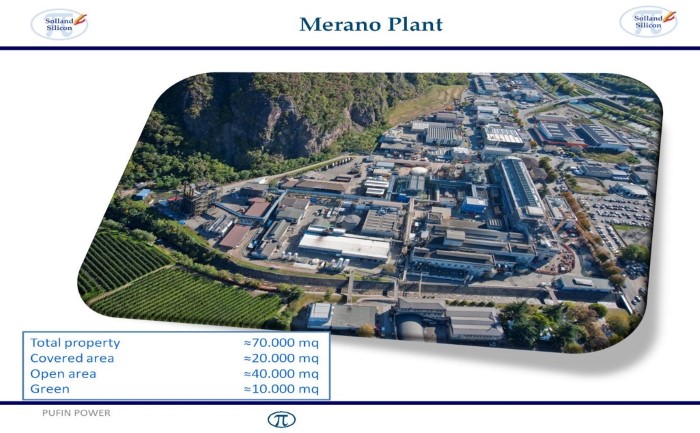
Solland Silicon is one of the pioneers in the process fieldbus area and has been operating plants with PROFIBUS since the mid-1990s. Polycrystalline silicon is produced in Meran. A new ultra-modern plant expansion was made and put into service from 2008 to 2010. Based on positive experience, the company chose the field-proven PROFIBUS technology for this.
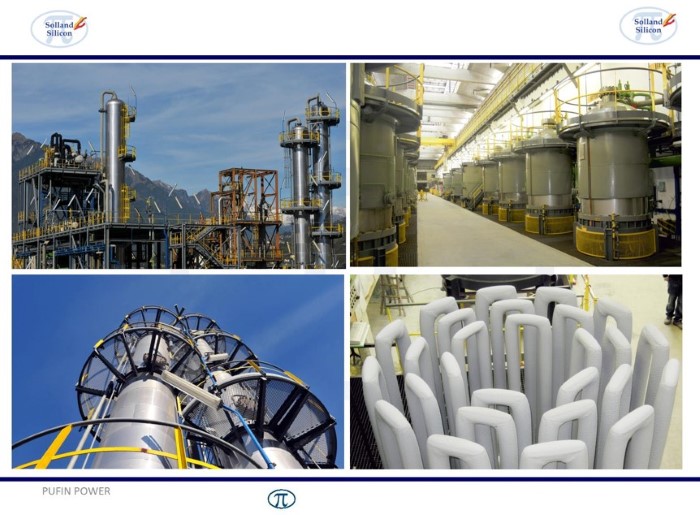
But first things first – some history:
During the last two decades Solland Silicon gathered experience with PROFIBUS and was able to generate significant competitive advantages as a result. The implementation of PROFIBUS at Solland Silicon began back in 1996 when it was selected as the process fieldbus for a pilot project.
Through the use of PROFIBUS, the following savings were anticipated compared to the use of conventional 4…20 mA technology:
- Configuration cost -30%
- Hardware: -70% (control cabinets, I/O cards, Ex-barriers, distributor boxes, cabling)
- Software: -40% (configuration)
Because the pilot project was successful, 4 distillation columns were upgraded from pneumatic and 4…20 mA technology to PROFIBUS just one year later. Because the overall control system at that time could only handle Modbus, a protocol converter from Modbus to PROFIBUS was used. The advantage of this gateway solution was that it enabled a subsequent upgrade of the overall control system to PROFIBUS without significant expense. Thus, the plants with PROFIBUS could easily be integrated into the existing automation landscape step by step.

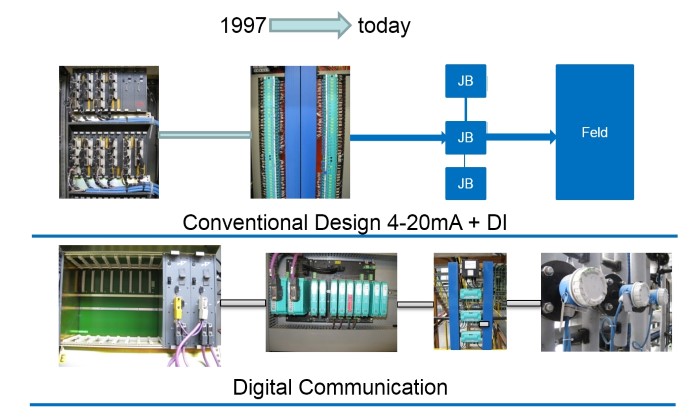
In the years that followed, it was demonstrated that this PROFIBUS plant had long-term stability and was easy to maintain. When an extensive plant expansion was made to the Meran factory from 2008 to 2010, widespread use of PROFIBUS, including various redundancy concepts, was chosen based on the good experience.
Key data of the expansion:
- Time period 2008-2010
- Investment approximately EUR 250 million ($274,000,000)
- 14 new plants:
- Distillation columns
- Hydrogen purification plants
- H2 and HCl compressors
- Production of N2 (on-site)
- New reactor hall
- Cooling water plants for the reactors
- Plants for recovery (condensation) of process gases (to -90°C)
- Highest demands for availability
Approximately 90% of the plants require an Ex version for Zone 1 or Zone 2.
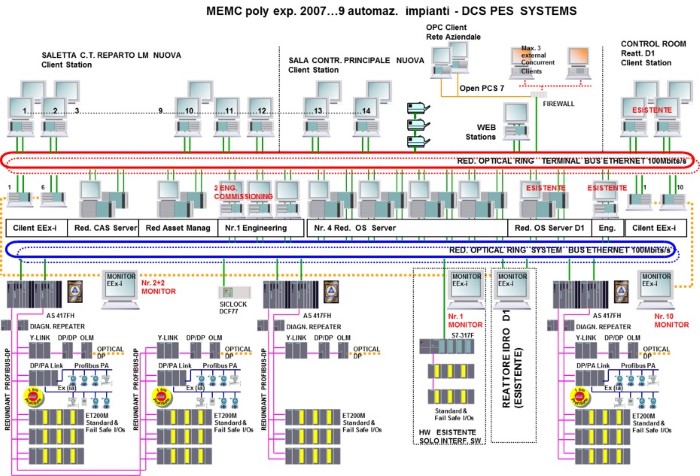
SIL3-capable overall control systems were used for the plant control. Specifically, the ABB 800xA System with 13 control units with AC800M-HI (redundant) and the Siemens PCS7 System with 26 control units with CPU 417FH (redundant) are being used.
The controllers of the various packages (compressors, etc.) were connected redundantly to the overall control system with PROFIBUS DP. All transmitters (pressure, temperature, etc.) and actuators were implemented in PROFIBUS PA (except in the SIL loop).
For easy and efficient proof of explosion protection, the FISCO concept was used for configuring and implementing the PROFIBUS lines.
To ensure high plant availability, all PROFIBUS DP lines are implemented with redundancy. The PROFIBUS PA lines are also redundant down to the segment couplers (Pepperl+Fuchs, SK3).
The overview of the utilized network components shows that Solland Silicon was able, thanks to the open PROFIBUS, to use the most suitable products from various manufacturers – with excellent interoperability:
- Master: redundant, integrated in the overall control system
- ABB 800xA with AC800M-HI (13 control units)
- SIEMENS PCS7 S7-417FH (26 control units)
- Segment couplers: Pepperl+Fuchs SK3 (18+16 units) gateway redundant with diagnostic module, redundant modules for segment voltage supply
- Surge protectors (104 units): Overvoltage protection of the PB segments
- MFT (60 units) = Multi-function terminal: Disconnecting module between trunk and field barriers (for explosion protection Zone 1)
- Field barriers (320 units): Pepperl+Fuchs F2D0-FB-Ex4
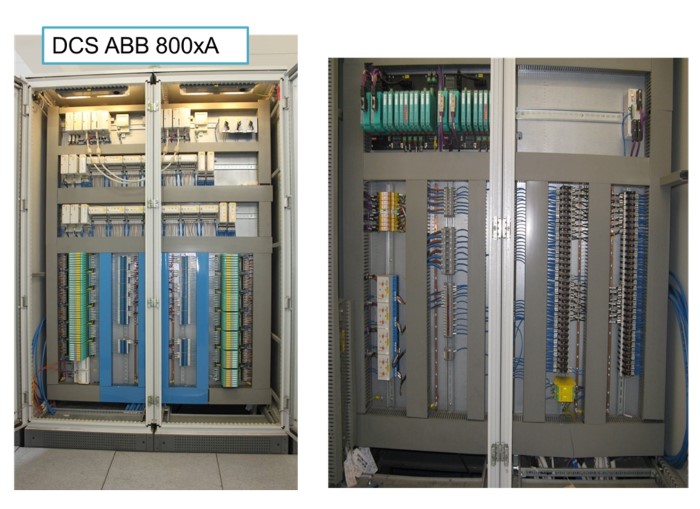
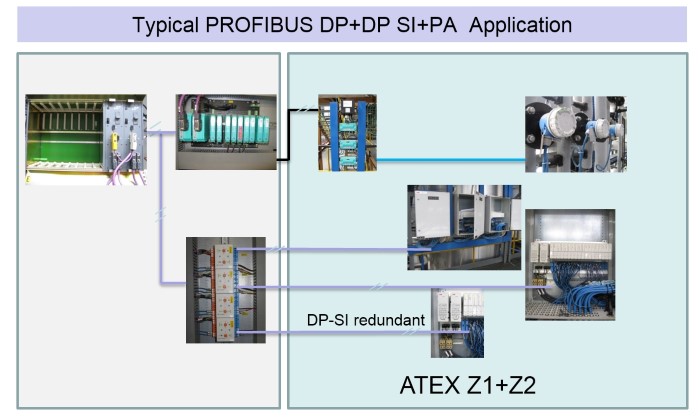
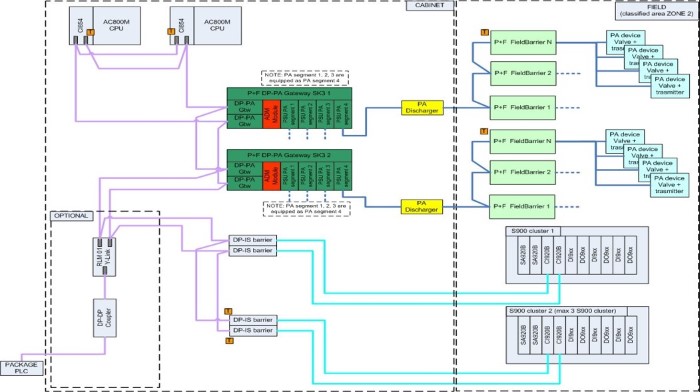
The same applies to the measuring technology used, since Solland Silicon was also able to select the most suitable devices from the portfolios of various manufacturers. In order to provide an overview of the plant complexity, the measuring points are listed in the following:
- Approximately 750 measuring devices in PROFIBUS PA
- Approximately 60 PROFIBUS DP slaves
- 12 inverters for drives up to 315 kW
- 24 remote I/Os in PROFIBUS DP with barriers
- 3500 DI/DO (std. and safety)
- 2600 PROFIBUS signals with remote I/O
For smooth operation of the plant, Solland Silicon makes use of the numerous advantages of the PROFIBUS fieldbus technology. The overall control system software and other software tools (E+H FieldCare) use DTM technology, which facilitates configuration and expands the diagnostic capabilities conveniently from the control room.
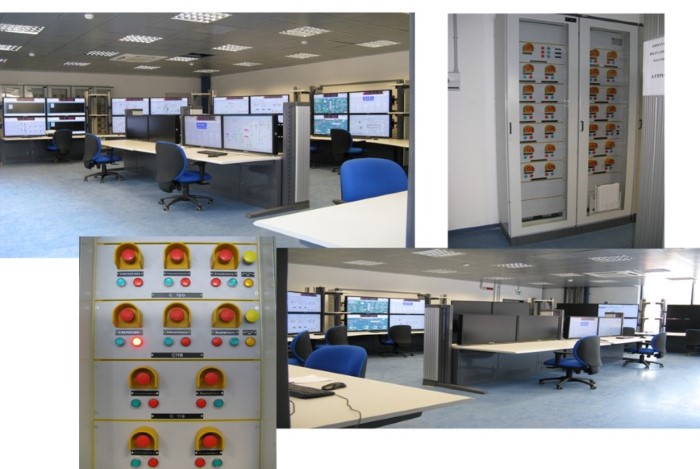
The monitoring of the signal quality (physical layer) of the PROFIBUS network (using P+F ADM module in SK3) permits a periodic, fast check of the health of the physical bus characteristics, which enables predictive maintenance:
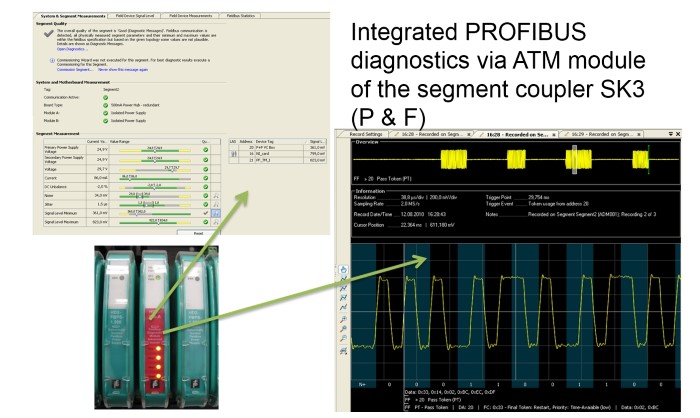
After 20 years of experience with PROFIBUS in its South Tyrol factory, Solland Silicon has found that PROFIBUS DP and PA have proven to be very reliable and that its expectation regarding cost savings have been met for the new plants (configuration cost: -30%, hardware: -70%, software: – 40%)!
The use of the DTM technology enabled a further quality improvement during configuration, parameter assignment, and diagnostics of the slaves and the network. The use of the FISCO concept made it much easier to prove explosion protection and also gave Solland Silicon flexibility for plant expansions and changes.
Moreover, the failure rate of components is very low and the replacement of defective devices is very easy. Solland Silicon has also discovered that troubleshooting and plant maintenance is much more effective and efficient than before, because modern tools greatly simplify the work of the plant operators and maintenance personnel.
Through the redundant implementation of the PROFIBUS DP lines, Solland Silicon was able to ensure very high plant availability over the years.
And the story continues: Initial applications with PROFIsafe and PROFINET have been implemented and are already in active operation at the factory in Meran. As the next step, the Motor Control Center (MCC) and Power Control Center (PCC) will now be equipped with PROFIBUS in order to take advantage of the benefits of digitalization there.
Acknowledgement: We are very grateful to Mr. Georg Pichler (Automation Manager at Solland Silicon) and the Solland Silicon company for the information and images provided.